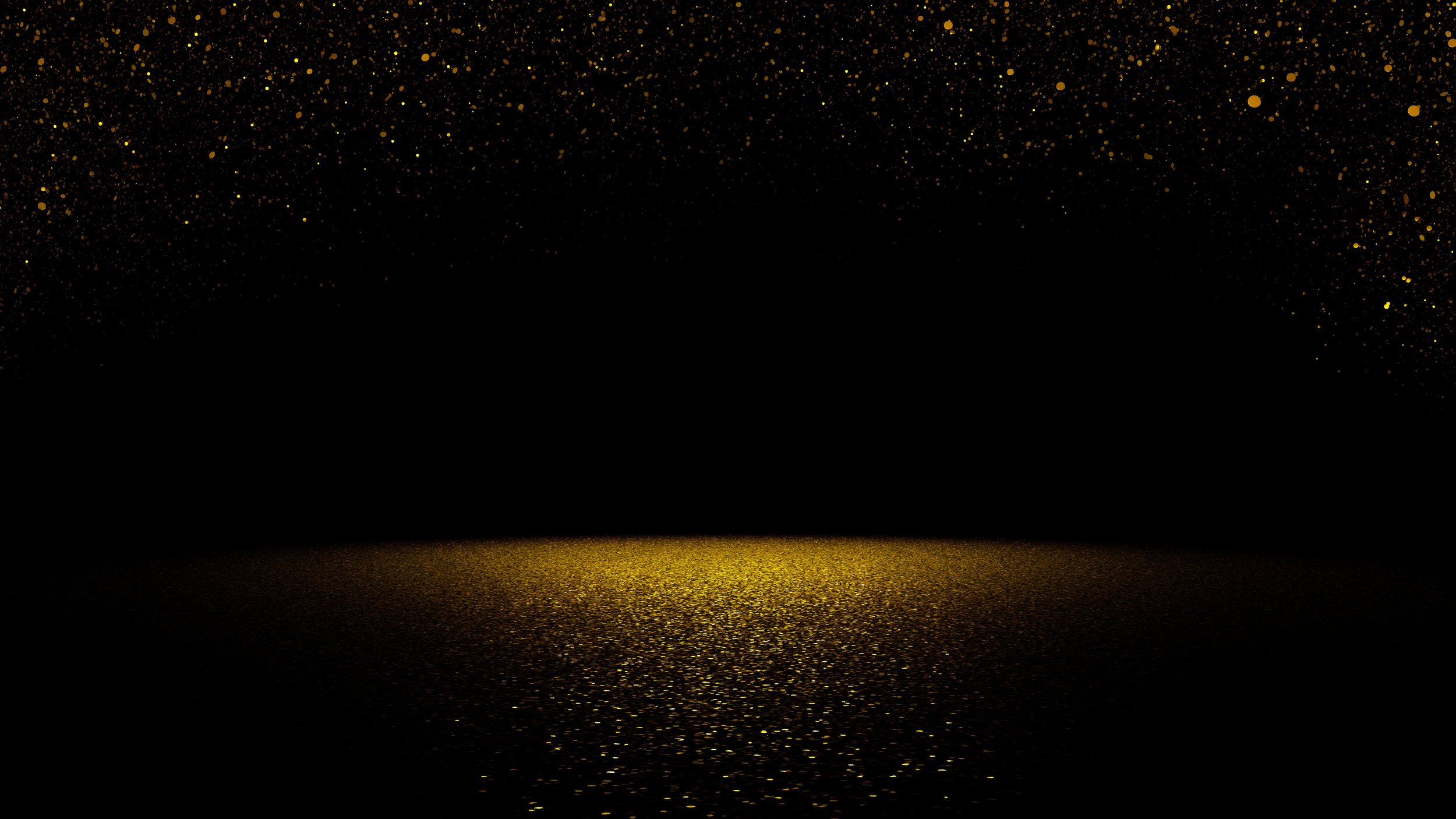
Multi-Chamber
Coating Systems
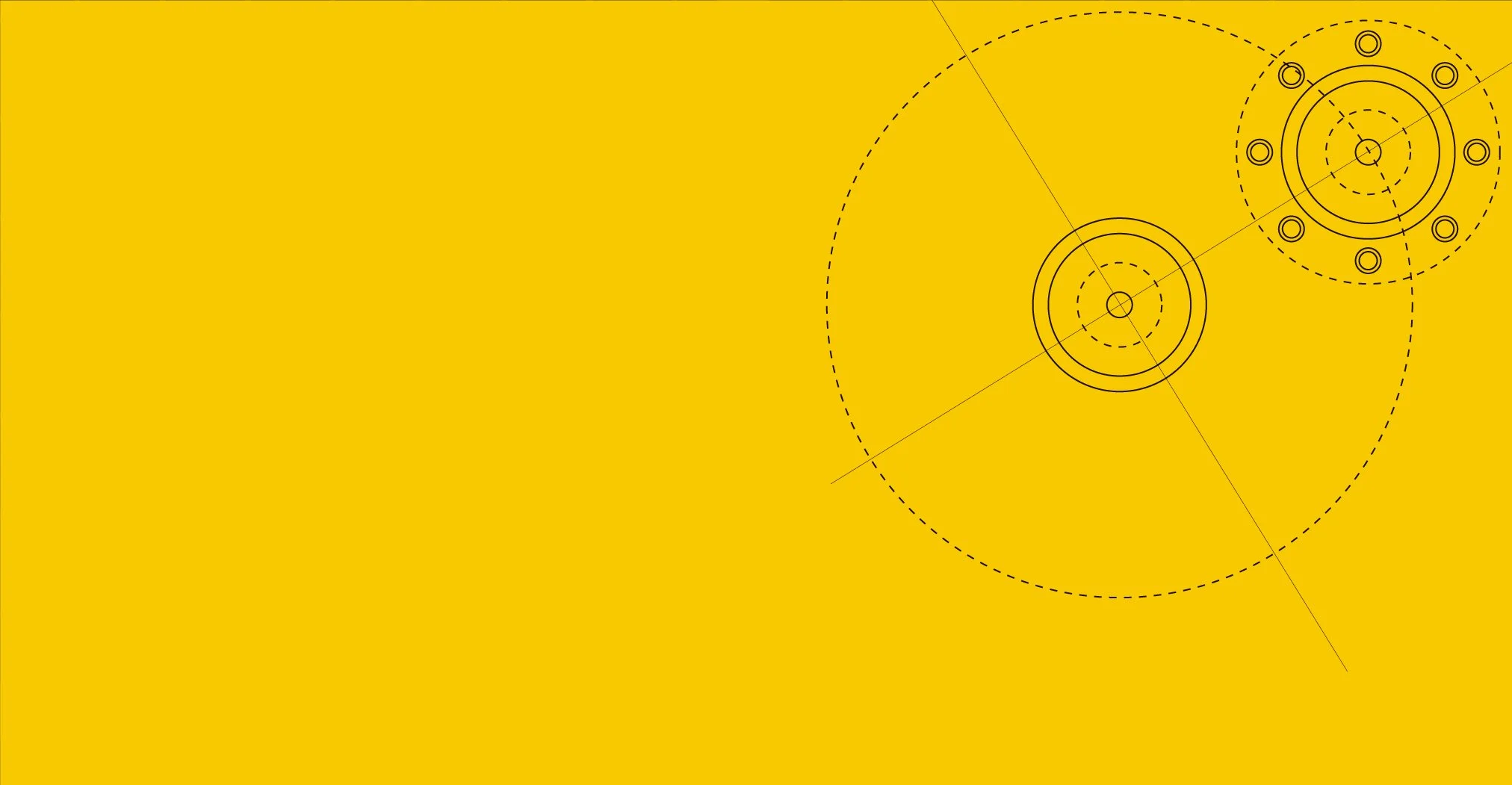
AJA International Multi-Chamber Systems are a great solution when your process requires various deposition techniques without exposing your substrate to atmosphere, and minimizing cross contamination. This results in enhanced performance and reliability since the individual chambers are optimized for a specific process, and many utilizing standard design features that have been field tested for decades. Systems can be equipped with magnetron sputtering, electron beam evaporation, thermal evaporation, ion milling, and various in-situ analytics (Ellipsometry, RHEED, MOS, etc.). The AJA International Multi-Chamber System can be configured in a linear, right angle, or in-line orientations, utilizing common load-locks, direct connection (chamber to chamber), or in-line UHV transfer tube. These systems can be designed with manual or automated transfer and built in HV or UHV configurations.
Multi-Chamber techniques employed include:
Magnetron Sputtering
E-Beam Evaporation
Thermal Evaporation
Ion Milling
Ion Beam Deposition
Pulsed Laser Deposition
Ellipsometry
Rapid Thermal Anneal
Oxygenation and Nitridization
XPS/AUGER/LEED Analysis
MBE
RHEED
MOS
SIMS
RIBE
The ATC-1800 UHV Electron Beam Evaporation System with Load-Lock and Appendage Chamber
This ATC-MC Multi-Chamber System has a unique combination of capabilities. The main deposition chamber includes a UHV 6-Pocket 15cc Linear Electron Beam Gun, and 4” motorized tilting (+/- 180 degrees) substrate holder with LN2 cooling capabilities. The load-lock system at natural static oxidation capabilities ranging between 5-100 Torr.
The custom appendage chamber has sample cleaning and analytical capabilities. For sample cleaning the chamber is equipped with substrate heating to 850C for sample degas, and a Hydrogen Atom Beam Source (HABS). The HABS is a thermal gas cracker that produces an absolutely ion-free hydrogen gas beam, avoiding ion induced damage to the substrate. For analytics the chamber is equipped with a HIDEN Temperature Desorption Probe (TPD/TDS). The TDS includes a triple filter mass analyzer configured with a cooled shroud giving the analyzer optimum sensitivity with minimum background contributions to accurately read contaminates being desorbed from the sample surface. In addition, the chamber is equipped with a RHEED and AUGER system from STAIB Instruments. When used in combination this will provide a wealth of complementary structural and chemical information to optimize thin film fabrication and better control of material properties.
ATC-MC Multi-Chamber Magnetron Sputtering System with Cassette Loading and Automated Transfer Capabilities
The ATC-MC Multi-Chamber Magnetron Sputtering System allows automated in-situ transfer between two UHV deposition chambers each equipped with (5) 3” con-focal sputtering sources, (1) 6” direct sputtering source, and (1) 4cm gridded DC ion source. Sputtering sources are powered by DC, RF, and HiPIMS generators.
System is designed for up to 8” wafer handling, 800C heating, 0-40 RPM azimuthal rotation, RF/DC biasing, and 100mm z-motion adjustment. Additional features include custom bakeout jacket for chamber conditioning (< 9.0x10-10 Torr), turbo/cryo pump combination, automated crystal monitor positioning for rate calibration and data logging, and post wafer cooling via He gas.
Dual ORION UHV with
Common Load-Lock
System features both sputter and evaporation process chambers with (10) A315-O 1.5" UHV sputter sources, (1) 6-pocket 15cc UHV linear e-gun, (4) Resistive Thermal Sources, 850°C rotating substrate heaters with RF bias, secondary tilting/cooled stage, RHEED, computer control, load-lock cassette with in-situ mask exchange for 4" diameter substrates and chamber to chamber transfer system.
ATC -MC-HY Multi-Chamber Hybrid Deposition Tool with UHV Transfer Tube & Glovebox Interface
The ATC-HY Multi-Chamber Hybrid Deposition Tool combines two Hybrid Process Chambers, each featuring e-beam and thermal evaporation, confocal magnetron sputtering, ion beam etching with a 360 degree tilt, and a water-cooled substrate holder. In addition, a third process chamber features post anneal, oxygenation and ashing capability. All are connected via a UHV magnetic transfer tube with sectional isolation, integral load-lock and glovebox compatibility.
Dual ATC/Orion Series UHV Sputtering System
The dual UHV Sputtering System above allows transfer between deposition chambers without exposure to load-lock pressures. Common 2-position load-lock chamber (e10-7 Torr) is located on the far right, oxide chamber (e10-8 Torr) in the center, and UHV sputter chamber (e10-10 Torr) with bakeout jacket on the left. The UHV chamber includes both con-focal and direct sputtering optimized for deposition of superconducting Nb films. The oxide chamber includes (5) con-focal 2” sputtering sources, O2 plasma source, and both static and dynamic natural oxidation capabilities.
ATC UHV Dual Sputtering & Electron Beam Evaporation Chamber
Dual UHV ATC 1800/2200E (Sputter/ E-Beam) system with (4) A320-XP 2 " UHV sputter sources with in-situ tilt, (2) 4-pocket 15cc UHV linear e-guns, RF ion source, 1200 l/s turbopumps, 850°C rotating substrate heaters with RF bias, computer control, and common vertex load-lock for 100 mm Ø substrates.