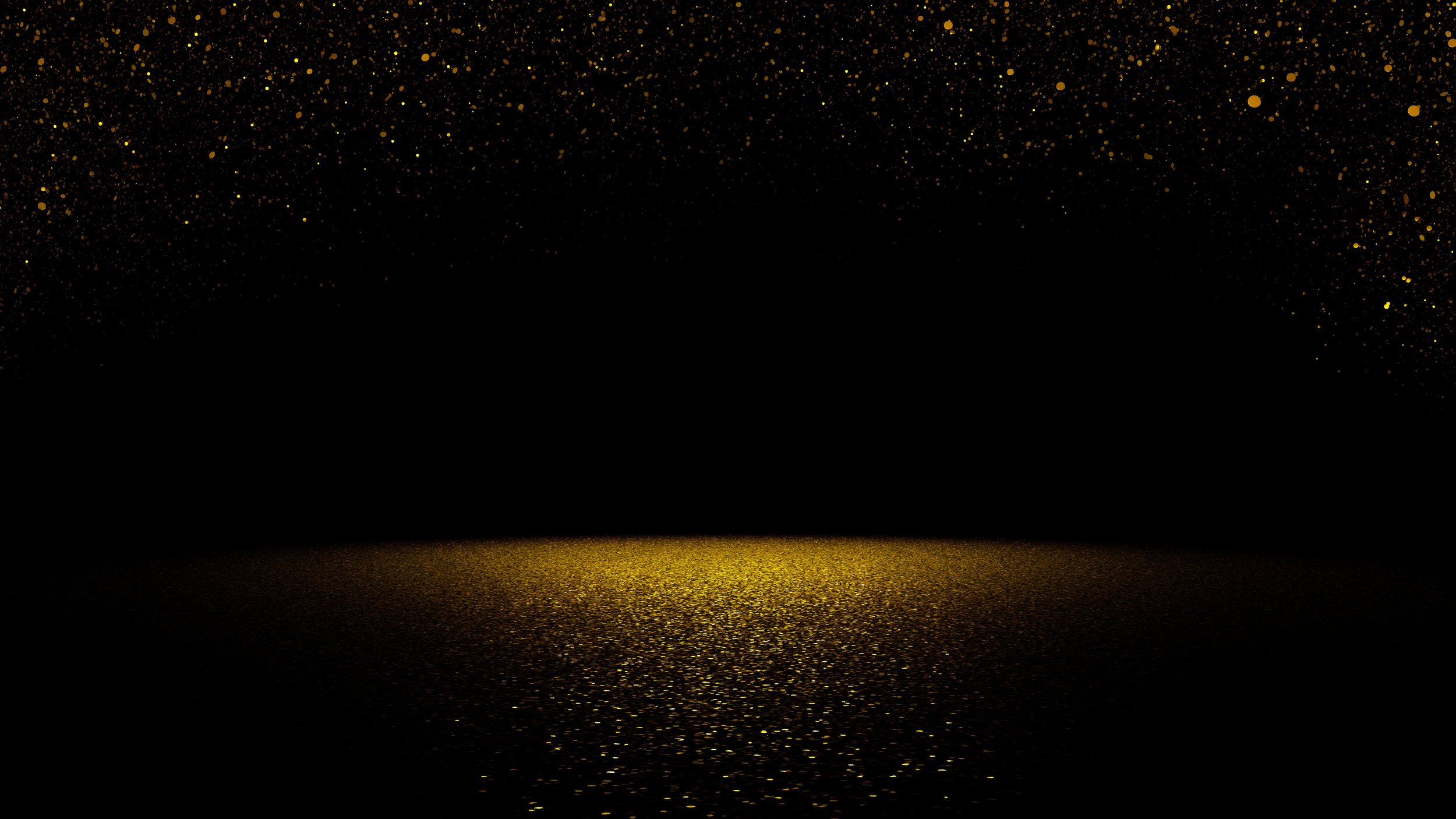
Orion Series
Sputtering Systems
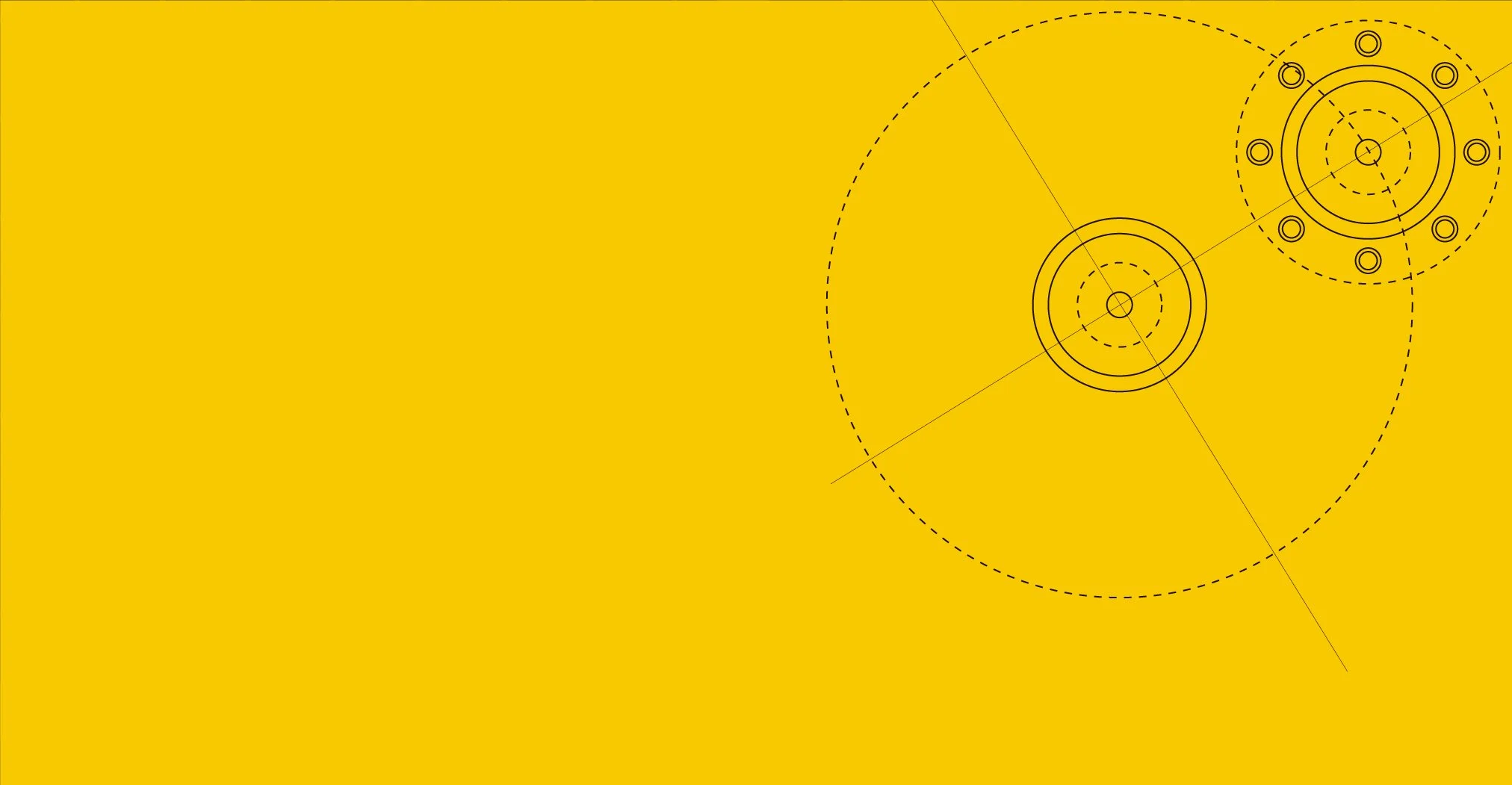
General Information
AJA International Orion Series Sputtering Systems are compact versions of the popular ATC Flagship Series physical vapor deposition tools designed to deliver maximum performance for limited budgets. These HV and UHV systems inherit many design features and common parts from the highly evolved ATC sputtering tools. The standard Orion modules (chambers, frames, cluster flanges, etc.) are generally in stock at AJA thereby reducing delivery times.
These popular systems use AJA’s exclusive Stiletto (HV) and A300-XP (UHV) magnetron sputtering sources (2” and 3”) and can be fitted with heating and cooling stages to accommodate substrates up to 6” Ø. Substrate temperature ranges from cooled LN2 to 1000°C are available depending on size and configuration.
Orion Systems feature a number of source configurations capable of accommodating up to (8) 2” sputter sources, (5) 3” sputter sources, and (4) 2” magnetron sputtering sources with in-situ tilt capability. Custom configurations are also available combining sputtering (con-focal or direct), thermal, ion sources, and in-situ analytics all on a single cluster flange. Orion Systems can also be easily connected to each other or to other ATC Systems for multi-chamber (e.g. metal/oxide) or multi-technique (e.g. sputter/evaporation/PLD/ion milling) configurations.
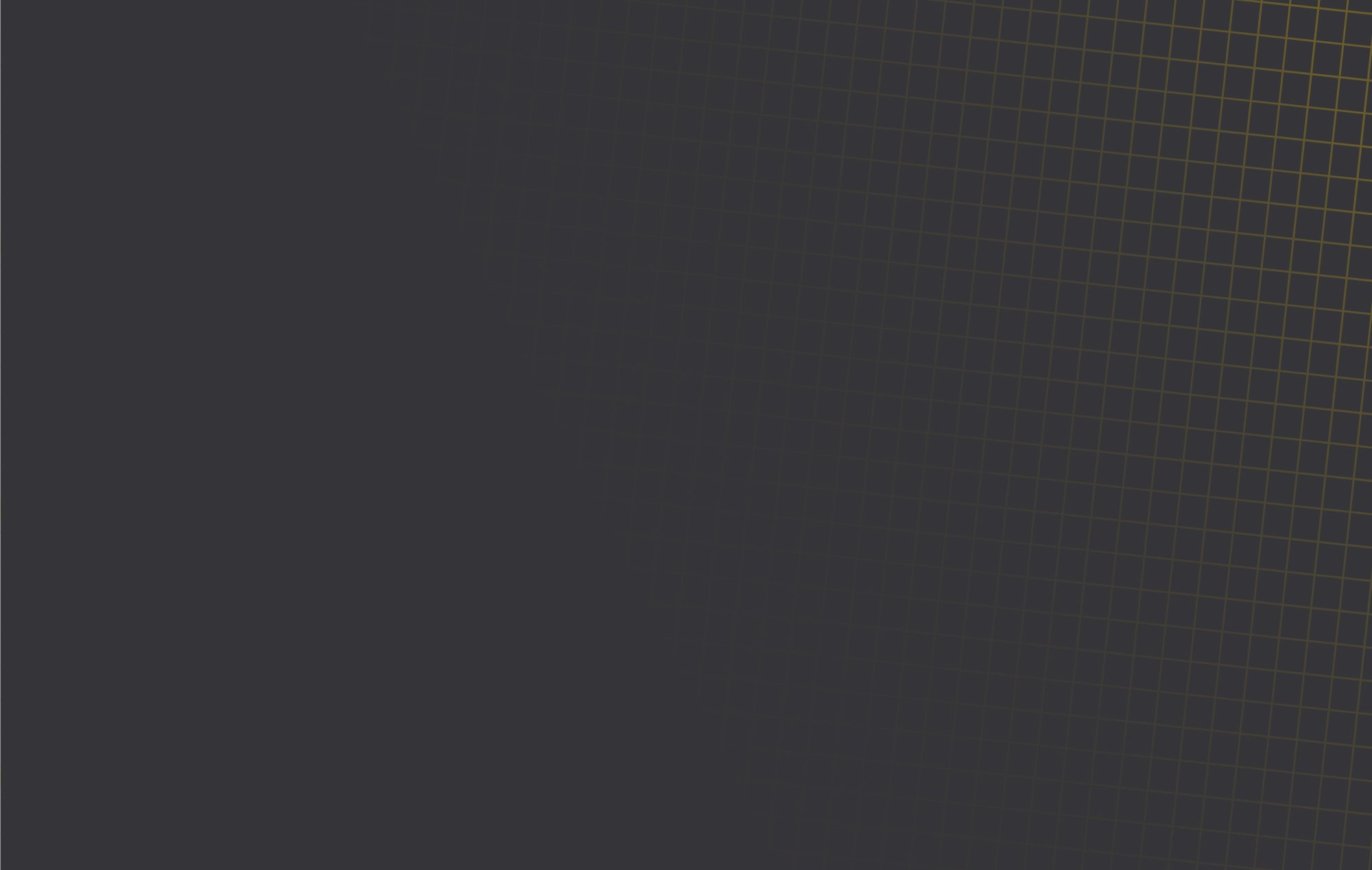
Magnetron Sputtering Source Cluster Flanges
AJA’s Stiletto-O (HV) and A300-XP-O (UHV) magnetron sputtering sources (2” & 3” target sizes) are designed specifically to fit cluster flanges for the compact Orion Systems. They feature tunable isolation chimneys with gas injection and flip-top shutters to accommodate compact spaces and custom chimney designs. The magnetron/cathode assembly is identical to the unique AJA A300 Series modular magnetrons which are used in the flagship ATC systems. The magnet array can be configured by the customer to operate in the nearly-balanced, unbalanced and magnetic material modes. Due to the compact design, the complete shutter, isolation chimney and ground shield assembly are quickly removed with only two screws for easy target access.
ORION 8-Ⅱ CLUSTER FLANGE
Flange accepts up to (8) 2” sources with both con-focal and direct sputtering capabilities
ORION 8-Ⅲ CLUSTER FLANGE
Flange accepts up to (5) 3” sources to allow uniform coatings over 6” diameter substrates.
CUSTOM ORION CLUSTER FLANGE
Customized flange with (5) 2” UHV con-focal sputtering sources, (1) 4cm Gridded DC ion source, and (1) thermal evaporation furnace.
ORION 8-Ⅱ T CLUSTER FLANGE
Flange accepts up to (4) 2” UHV sputtering sources with in-situ tilting capabilities.
Deposition of SiO2 from one 2" A320-XP magnetron onto a 100mm diameter Si wafer at 150 Watts, 3mTorr, 140mm working distance. Uniformity is +/- 2.08%.
Typical Rate/Uniformity Data
The Orion Series Sputtering Systems feature a con-focal sputter source flange oriented at specific angles determined from many decades of experience with the in-situ tilt sources found on the flagship ATC systems. The specially designed chimney/ground shield/shutter system allows a high degree of deposition uniformity over substrates more than twice the target diameter. A typical deposition profile with SiO2 on a 4” diameter Si wafer is shown.
Deposition rate is a function of sputter yield of the material, maximum allowable power density into the target (depends on heat transfer capability of target material), and type of power used (e.g. RF, DC, pulsed DC, and HiPIMS).
Maximum deposition rates are achieved with materials such as Au, as this material has a high sputter yield, excellent heat transfer, and can be sputtered with DC (most efficient).
Slow deposition rates can be expected with materials such as Al2O3, as this material has a very low sputter yield, poor heat transfer, and must be sputtered with RF (1/2 the efficiency of DC). Typical rates are 0-18 Å/sec with Au, 0-9 Å/sec with Cu and 0-0.16 Å/sec with Al2O3 in a confocal configuration with 2” sources on a 100 mm Ø substrate.
Direct deposition at short working distances (50-100 mm) can achieve higher rates. However, con-focal geometry results in much better uniformity, the ability to co-deposit alloy films, and the ability to grow better ultra-thin film multilayers, since the substrate is always “in the plasma.” The cost of the smaller targets employed in con-focal configurations can also significantly reduce operating costs.

Substrate Holders - Heating/Cooling
The con-focal Orion systems utilize motorized, rotating substrate holders to achieve excellent uniformity, allow the co-deposition of alloy films, and facilitate the deposition of pristine, ultra-thin film multilayers since the substrate is always “in the plasma.” Substrate heaters are available to reach up to 1000°C and feature reactive gas injection rings, RF/DC bias capability, in-situ manual or motorized Z motion (for working distance adjustment and load-lock transfer) and in-situ mask exchange (available only with certain configurations).
Cooled substrate carriers utilizing either water or LN2 are also available depending on the application requirement.
For combinatorial chemistry applications (simultaneously deposited gradient films), both heated and cooled substrate holders which do not require rotation during deposition, are offered.
A wide variety of custom substrate holders have also been designed, over the years.
Phase II-Au Computer Control
The AJA LabVIEW based Phase II-Au computer control system is used on all Deposition Systems. This straightforward, user friendly control system utilizes a large 22” articulating screen with wireless keyboard and mouse. The back panel of the hardware module is populated with connectors to interface to all aspects of the sputtering system and to allow for easy future "plug and play" upgrades/expansions.
The Phase II-Au control system allows the user to operate in either the “manual mode” or the “automated processing mode.” In the, “automated processing mode” the user designs "process layers” which are then compiled and saved as a “process” to be executed with a single command. The system allows up to 104 unique user entry points which are accessible only by password, limiting access to a user’s process layers and thereby preventing unexpected corruption of a user’s saved processes. Special “soak layers” can be easily incorporated into the process. Adjustable time base data-logging to a Microsoft Excel spreadsheet is standard. Remote preparation of new processes in a Microsoft Excel spreadsheet emulator format is available as an option.
The standard Phase II-Au control system will accommodate up to (5) DC power supplies, (4) RF power supplies, (1) 4-way DC switchbox, (1) 4-way RF switchbox, (4) process gases, (24) Valves/shutters, (1) DC ion source, down stream closed loop automatic pressure control, substrate rotation and substrate temperature control. Processes are aborted if plasma is not detected, substrate temperature, process gas or chamber pressure is out of range.