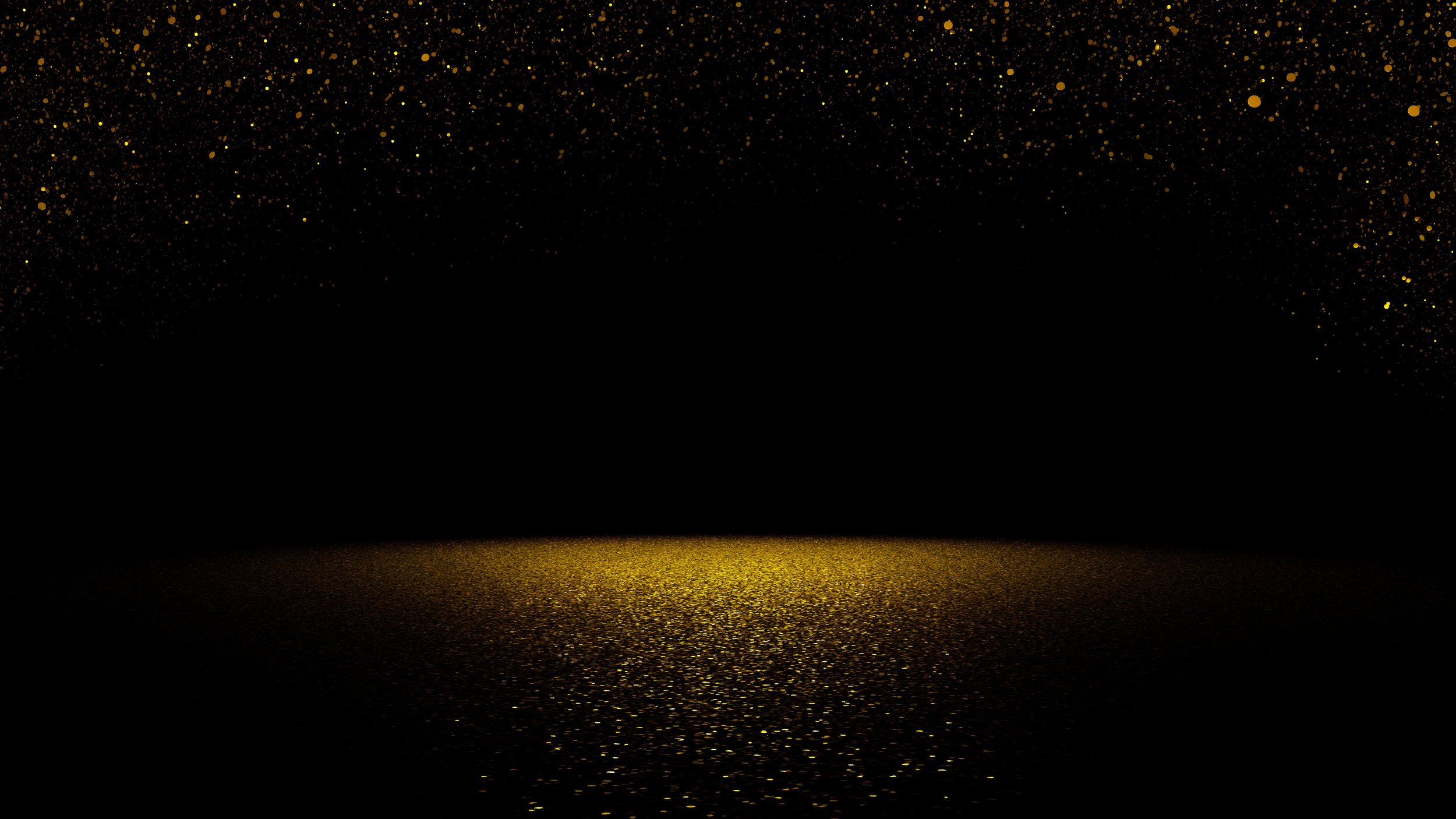
Batch Series
Sputtering Systems
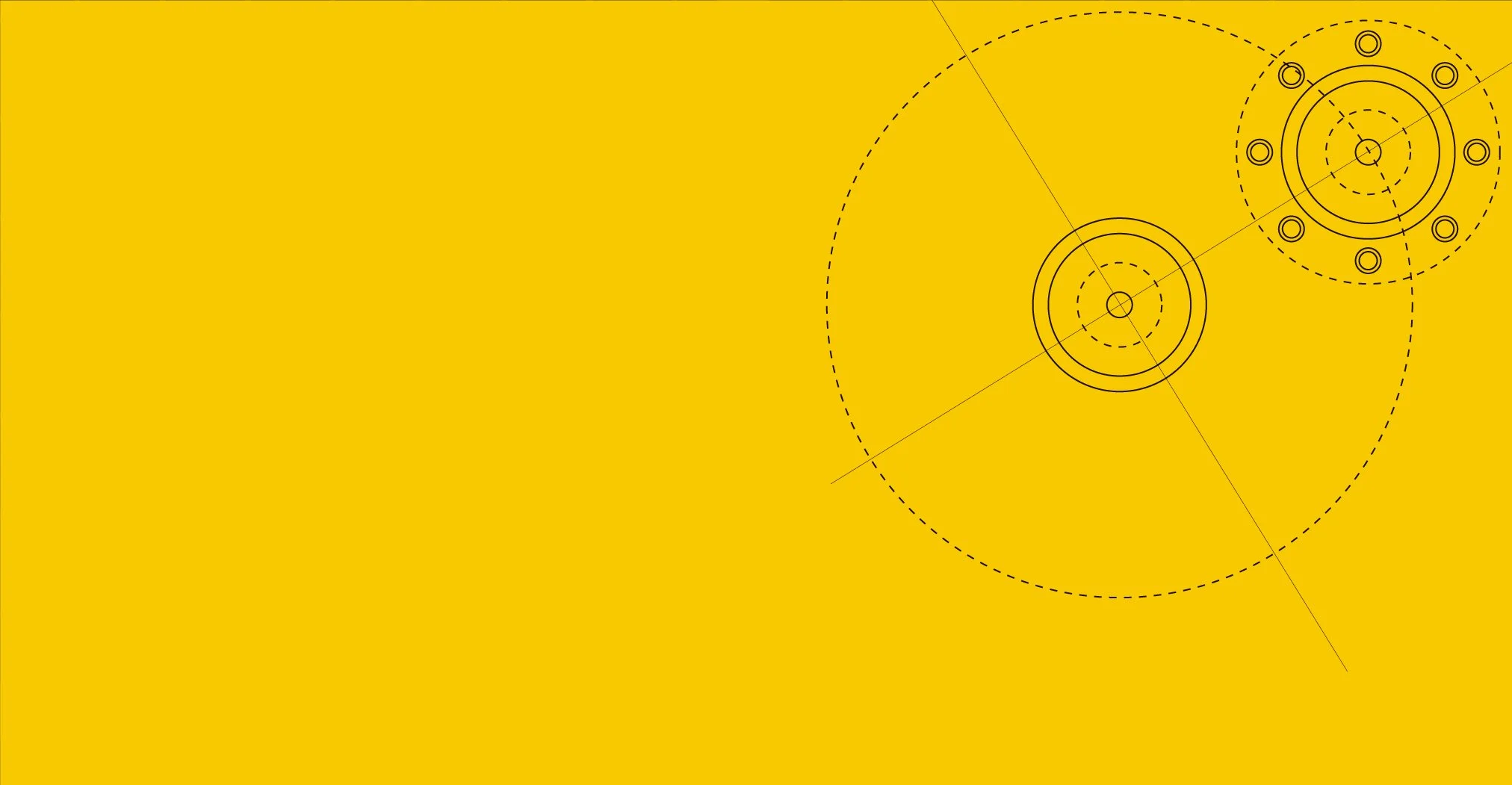
General Information
AJA International ATC-B Series Batch Coating Systems are custom engineered sputtering and evaporation systems built to handle smaller production runs of multiple substrates. Cylindrical or box style chambers are employed depending on the specific requirement. For extended process times, horizontal magnetron sputtering is most common since material build-up has no chance to fall onto the substrate or into the magnetron sputter source thereby aborting the process due to shorting.
To optimize these systems for a given PVD process, AJA engineers can draw on a long history of standard and custom sputter source and substrate holder designs to satisfy the specific needs of the application. For example, the ATC-B 3400-H horizontal cylinder has special magnetron sputter sources which are designed to reliably run a 50,000 layer processes that can take up to 4 days to complete.

Substrate Holders - Heating/Cooling
AJA has designed over 130 different types of customized substrate holders and fixturing for custom pilot production batch coating systems since 1991.
These include rotating, indexing, linear and planetary motion, plus heating, cooling and RF/DC biasing. Different aspects of these proven designs can be combined to create a new, yet highly reliable custom substrate holder. Reliable substrate holder design is one of the most crucial parts of a custom batch coater and manufacturer experience can easily account for the difference between a maintenance intensive machine and the high throughput machine everyone desires.
Phase II-Au Computer Control
The AJA LabVIEW based Phase II-Au computer control system is used on all Deposition Systems. This straightforward, user friendly control system utilizes a large 22” articulating screen with wireless keyboard and mouse. The back panel of the hardware module is populated with connectors to interface to all aspects of the sputtering system and to allow for easy future "plug and play" upgrades/expansions.
The Phase II-Au control system allows the user to operate in either the “manual mode” or the “automated processing mode.” In the, “automated processing mode” the user designs "process layers” which are then compiled and saved as a “process” to be executed with a single command. The system allows up to 104 unique user entry points which are accessible only by password, limiting access to a user’s process layers and thereby preventing unexpected corruption of a user’s saved processes. Special “soak layers” can be easily incorporated into the process. Adjustable time base Data-logging to a Microsoft Excel spreadsheet is standard. Remote preparation of new processes in a Microsoft Excel spreadsheet emulator format is available as an option.
The standard Phase II-Au control system will accommodate up to (5) DC power supplies, (4) RF power supplies, (1) 4-way DC switchbox, (1) 4-way RF switchbox, (4) process gases, (24) Valves/shutters, (1) DC ion source, down stream closed loop automatic pressure control, substrate rotation and substrate temperature control. Processes are aborted if plasma is not detected, substrate temperature, process gas or chamber pressure is out of range.