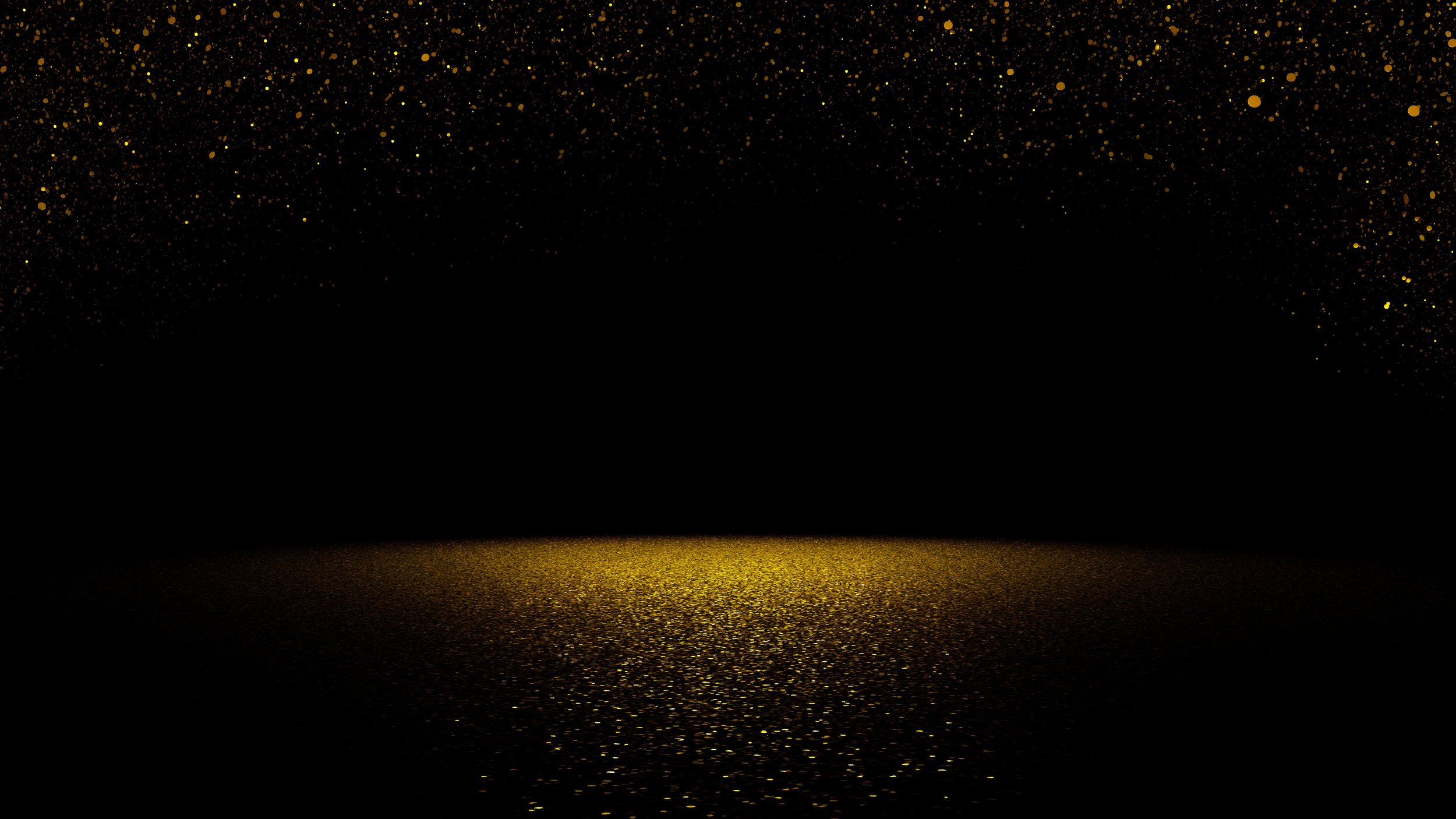
ATC-E HV Series
Electron Beam Evaporation Systems
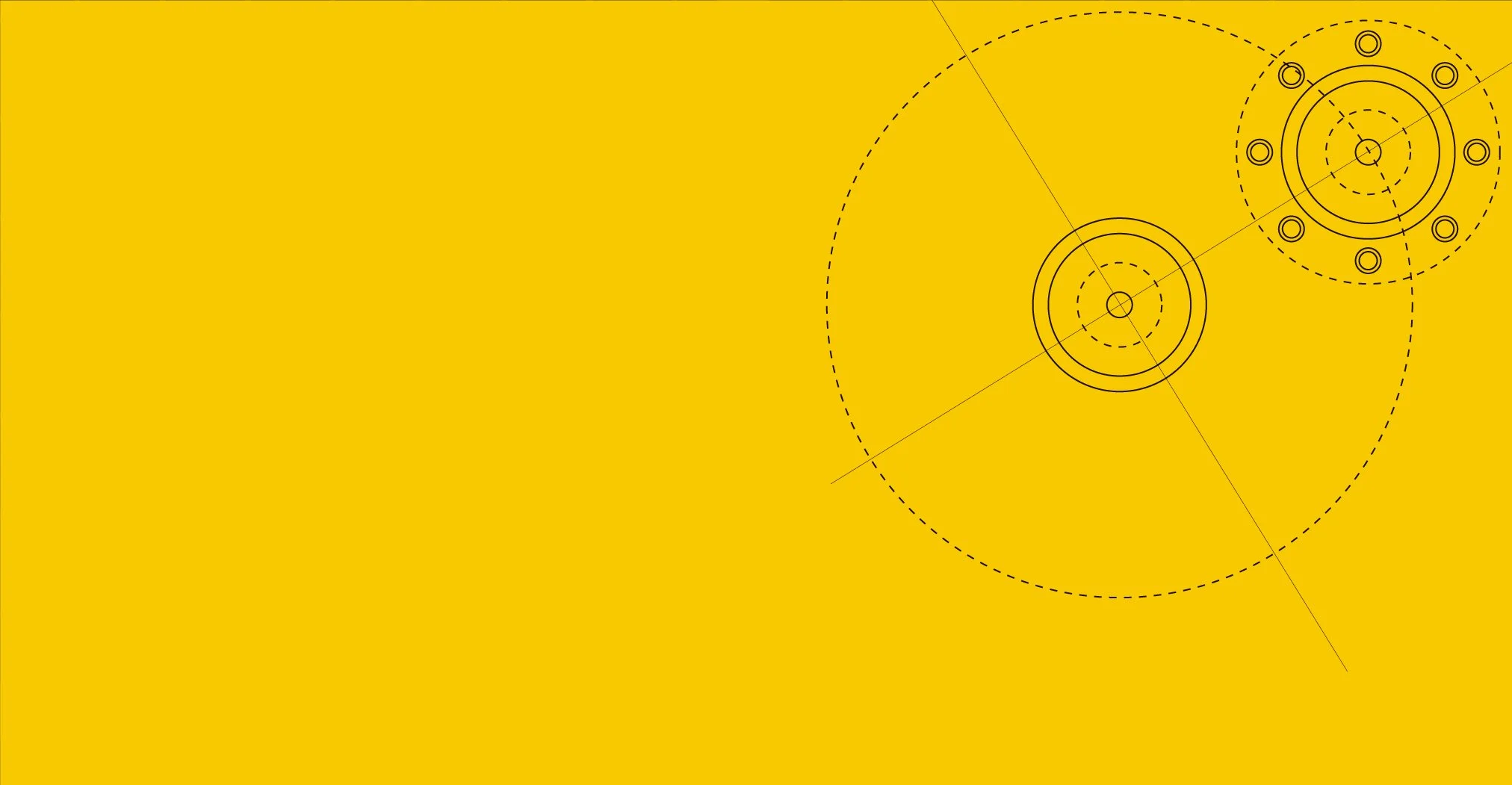
General Information
AJA International ATC-E HV Series Electron Beam Evaporation Systems are available in stainless steel, box-style chambers. These physical vapor deposition systems offer exceptional value while delivering optimal performance and utilizing top quality sub-components. They inherit many design features and common parts from the highly evolved ATC & ATC Orion sputtering tools and can be outfitted with a single or multi-pocket rotary e-beam source, thermal evaporation sources, ion / plasma sources, Knudsen cells, low temperature evaporation cells for organic materials and thermal evaporation furnace sources. In addition, these systems are available with load-locks, QCM control, heated or cooled substrate holders with tilting capability, planetaries, various pumping packages and automated control.
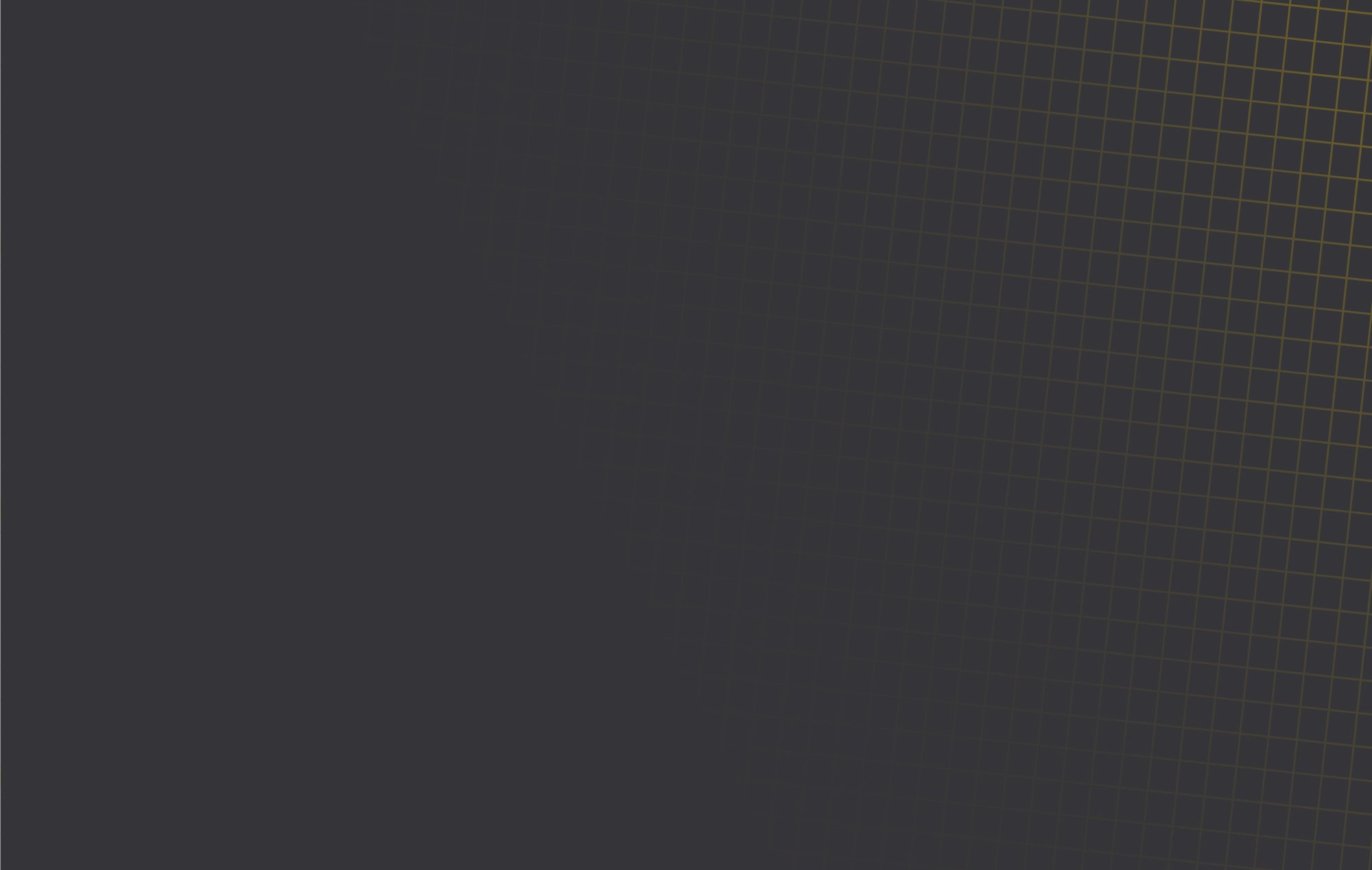
Evaporation Sources
AJA offers a variety of sources on our ATC-E Series Evaporation Systems. The box-style chambers are best suited for rotary e-beam sources which are bottom mounted with a large, double-hinged, easy access loading door for service and loading. Spare ports on the chamber bottom straddling the linear e-beam source allow for the addition of multiple secondary thermal evaporation sources. Secondary thermal sources are typically optimized for specific materials (e.g. organics) or to allow co-evaporation capabilities. With two or more evaporation sources, isolation shielding and individual shutters are included to minimize cross contamination.
6-pocket, 15cc rotary e-beam evaporation source with (2) secondary thermal evaporation sources
6-pocket, 25cc rotary e-beam evaporation source with isolation shielding
6-pocket, 15cc rotary e-beam evaporation source with (2) 1cc evaporation furnaces for low-temp organics
4-pocket, 7cc rotary e-beam evaporation source with (3) secondary thermal evaporation sources
Deposition of SiO2 with XY sweep on 200mm diameter Si wafer with simple, azimuthal rotation, run for 75 seconds at 8450V, 24 mA, 500 mm working distance.
Uniformity is +/- 0.7%.
Typical Rate/Uniformity Data
The ATC-E Series Evaporation Systems can be configured for high rate, low rate, multi-layer and co-deposition applications depending on the chamber, sources, substrate carrier and general configuration chosen. Proper power, crucible liner or boat material, soak, and XY sweep decisions must be made for each material to be evaporated to ensure the desired rates, stability and film characteristics. Typically, materials with good heat transfer properties (eg. Al) do not require XY sweep but may require a liner (Au) whereas materials with poor thermal properties (eg. Cr) tend to tunnel and spit unless the e-beam power is diffused with an XY sweep. Proper substrate fixturing is required to obtain the best uniformity.

Substrate Holders - Heating/Cooling
AJA can fit your customized evaporation system with a wide variety of substrate holders. Our substrate heaters can be equipped with azimuthal rotation, heating up to 1000°C, RF/DC bias capability and tilting in a single axis plane. Our cooled stages can be equipped with H2O or LN2 cooling in the static or rotational modes. Additional features include azimuthal rotation, RF/DC bias and tilting in a single axis plane. Substrate holders can be semi-automatic or fully automated depending on the process requirements. Custom configurations are also available when heating and cooling are required.
For batch coating applications domed-styled substrate carriers optimized for lift-off processing and planetary-style holders are also available. Process gas ring or gas distributor options are offered for reactive processing or applications requiring an anneal step.
Glancing Angle Deposition (GLAD) 4” Substrate
Holder with 800°C heating, rotation, and +/- 180° tilting
Glancing Angle Deposition (GLAD) 6" Substrate
Holder with water cooling, rotation, and +/- 180° tilting
Phase II-Au Computer Control
The AJA LabVIEW based Phase II-Au computer control system is used on all Evaporation Systems. This straightforward, user friendly control system utilizes a large 22” articulating screen with wireless keyboard and mouse. The back panel of the hardware module is populated with connectors to interface to all aspects of the sputtering system and to allow for easy future "plug and play" upgrades/expansions.
The Phase II-Au control system allows the user to operate in either the “manual mode” or the “automated processing mode.” In the, “automated processing mode” the user designs "process layers” which are then compiled and saved as a “process” to be executed with a single command. The system allows up to 104 unique user entry points which are accessible only by password, limiting access to a user’s process layers and thereby preventing unexpected corruption of a user’s saved processes. Special “soak layers” can be easily incorporated into the process. Adjustable time base Data-logging to a Microsoft Excel spreadsheet is standard. Remote preparation of new processes in a Microsoft Excel spreadsheet emulator format is available as an option.
The standard Phase II-Au control system will accommodate up to (3) DC power supplies, (3) RF power supplies, (1) 4-way DC switchbox, (1) 4-way RF switchbox, (1) DC Ion Source, (1) RF Ion Source, (1) Linear or Rotary Ebeam, (1) Deposition Controller, automatic selection of sweep pattern based on material, (4) process gases, (24) Valves/shutters, down stream closed loop automatic pressure control, substrate rotation, substrate tilting and indexing and substrate temperature control. Processes are aborted if plasma is not detected, substrate temperature, process gas or chamber pressure is out of range.