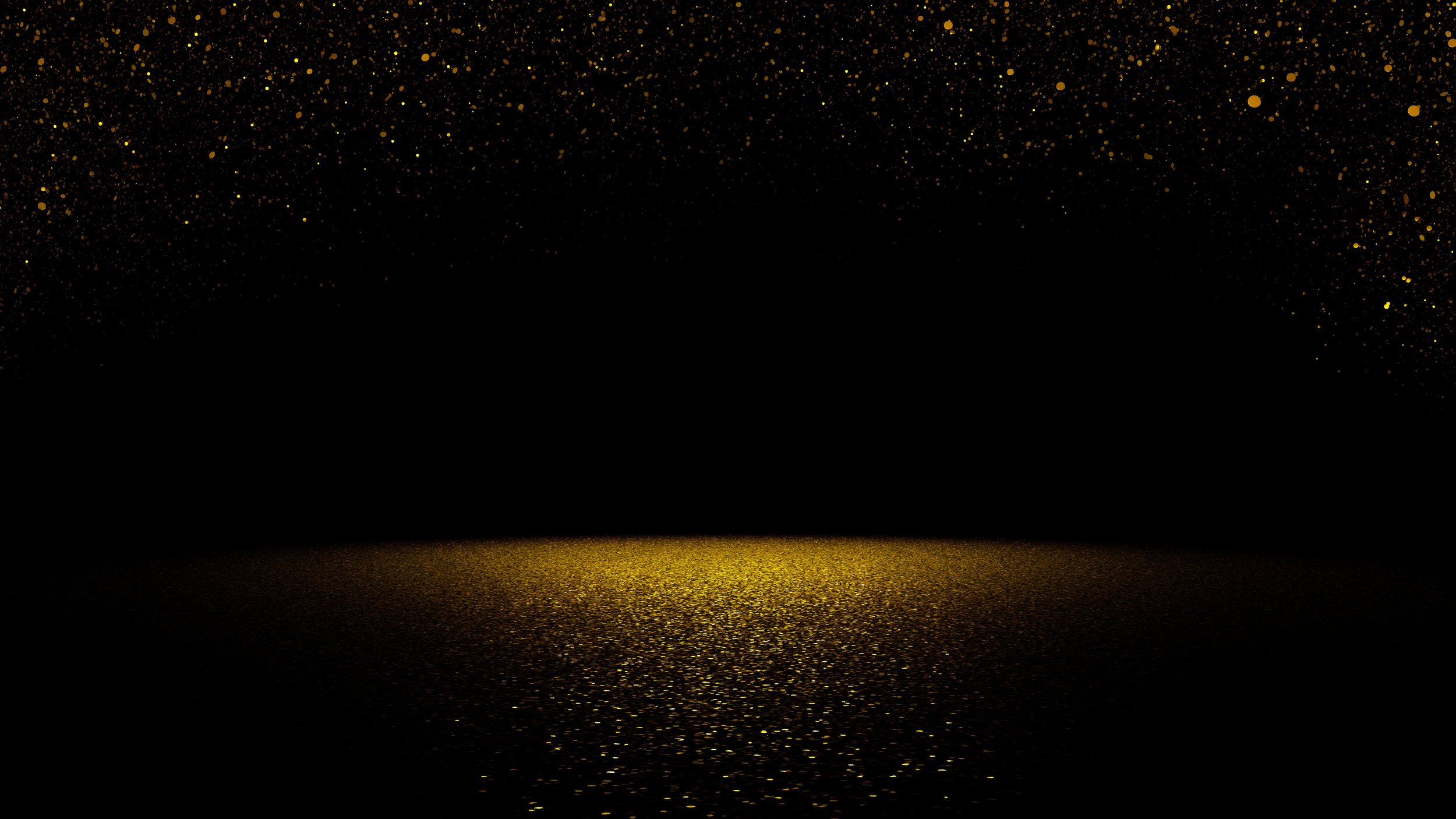
Orion IMS Series
Ion Milling Systems
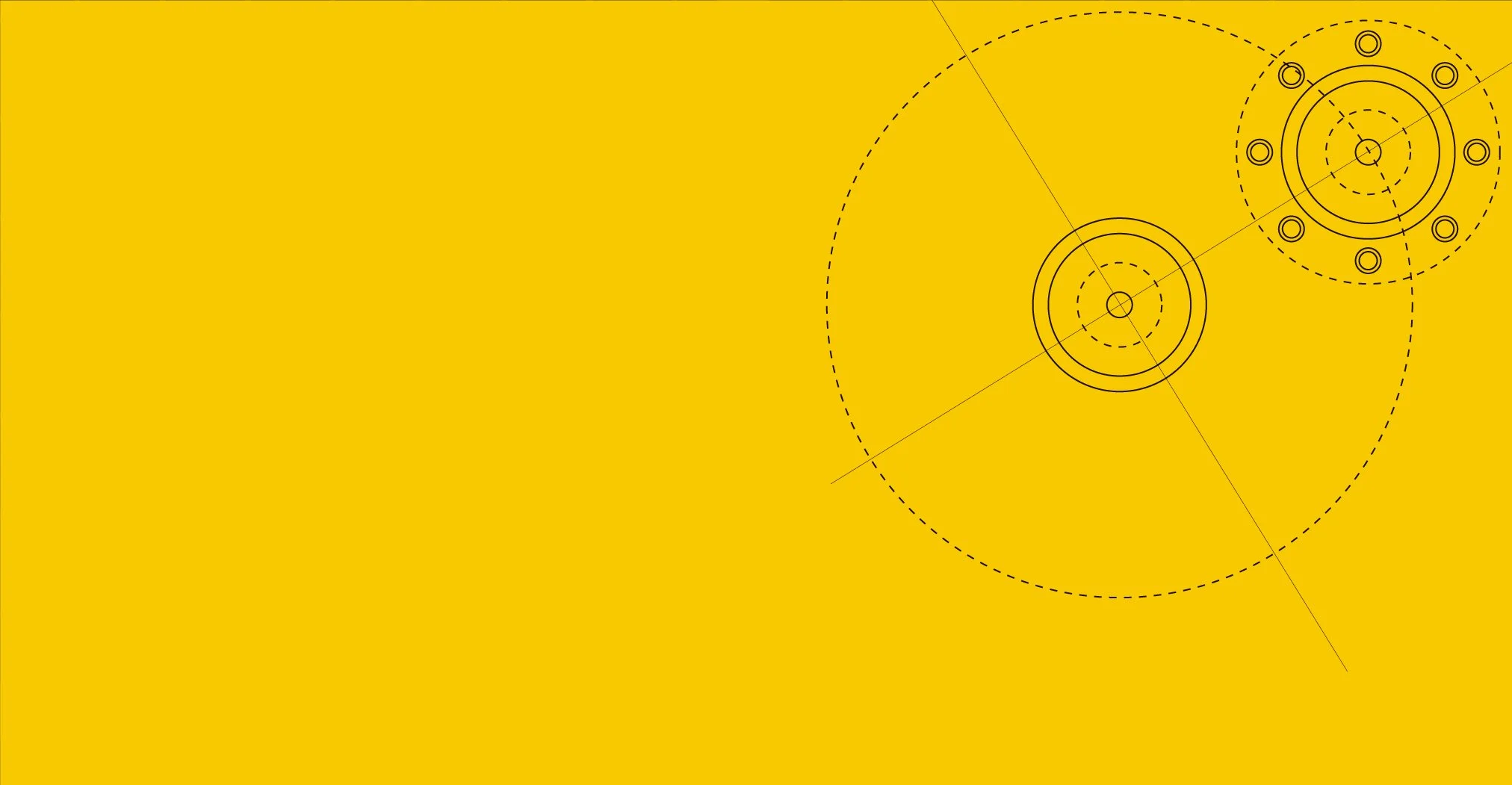
General Information
AJA International, Inc. ATC Orion Series Ion Milling Systems are durable, compact tools designed to deliver maximum performance for limited budgets. Chambers are cylindrical in design with a large hinged door for ease of access for operation and/or routine maintenance. System utilizes a substrate holder with up to 4” wafer handling with various capabilities including azimuthal rotation, motorized tilt adjustment, and cooling capabilities (H2O, LN2, Backside Gas Cooling). Additional features include sputter source(s) for passivation layers, SIMS end point detection, and gridded DC ion source ranging between 1-8cm in size.
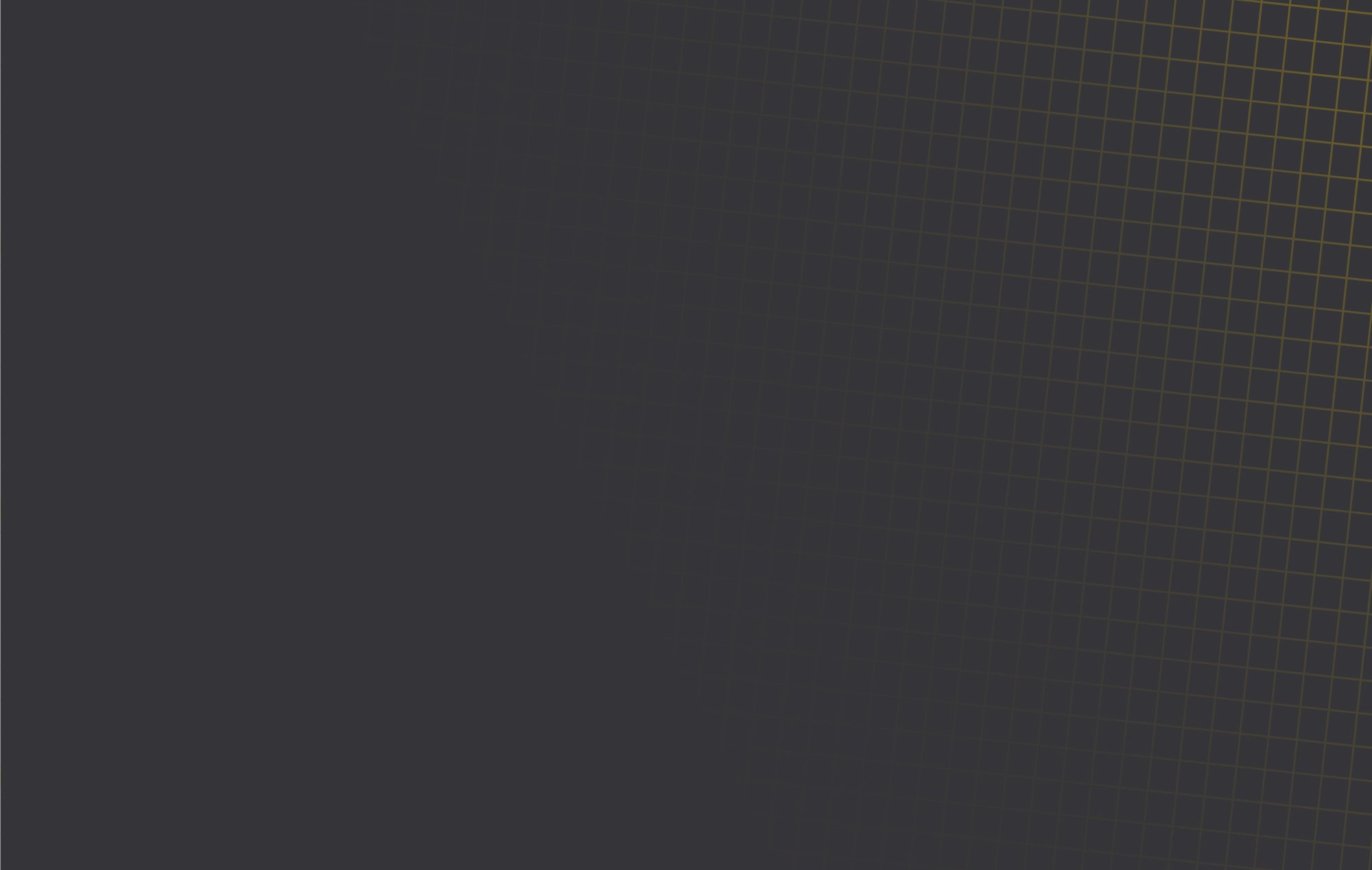
Ion Sources
AJA manufactures and utilizes the leading ion sources on the market in all of the ATC-Series Ion Milling Systems. Systems are fitted with either DC/RF Kaufman style sources for high rate applications or capacitively/inductively coupled RF ion sources with grounded grids for sensitive, low energy applications. DC sources are typically employed for non-reactive milling (Ar only) and include exposed filament neutralization. RF ion sources are compatible with inert and reactive gases. Depending on the application, sources can be positioned in the chamber for direct or angular incidence to the substrate.
Typical milling profile yielding +/- 2% uniformity with SiO2 on a 3" Ø Si wafer and using an angled, gridded Kaufman style ion source. This process also utilized a rotating, water-cooled, tilting substrate holder.
Typical Rate/Uniformity Data
The angle of incidence to the substrate affects the rate and uniformity. One of the many benefits to the eccentric, off axis milling configuration is the reduced ion source size necessary to achieve uniform etching of larger wafers which would typically require costly, larger sources to achieve similar uniformity results. Angular incidence also improves removal rates while reducing damage to the substrate.
In addition to the milling angle, ion beam energies are a key component of milling rates. Depending on the ion source selected, ion energy can vary from 50-1200 eV allowing for a wide range of milling applications. For heavier milling requirements, higher ion energies are commonly desired. Lower ion energies are better suited for more sensitive substrates.
During the milling process, an increase of the substrate temperature can affect the milling rate and composition of material. Stabilizing the substrate temperature during the milling process is desired in order to maintain a consistent rate and uniformity and prevent substrate damage or unwanted modification.

Substrate Holders
AJA designs and manufactures substrate holders for all ATC-IM Ion Milling Systems. Typical ion milling processes incorporate sample cooling. Heating of the substrate during ion milling may produce undesirable results ranging from non-linear etch rates to unwanted cross linking of polymers used in lithographic resists. On occasion, heating may be desirable to achieve a combination of chemical and physical etching (RIBE).
AJA UNO Series Substrate Holders
The AJA UNO Series Substrate Holders can accommodate substrates up to 4" in Ø with water cooling, rotation, and the ability to tilt up to +/- 180°. Substrates attach directly to the water cooled surface to maintain temperature stability during the milling process. A retraction system with a convenient slide rail and programmable, motorized incident angle control to within 0.1° is available.
The AJA UNO-SM-HCC Series Substrate Holders feature heating and cooling and reactive gas injection at the wafer surface along with programmable, motorized, incident angle adjustment. Both versions are vacuum load-lock compatible.
Phase II-Au Computer Control
The AJA LabVIEW based Phase II-Au computer control system is used on all Ion Milling Systems. This straightforward, user friendly control system utilizes a large 22” articulating screen with wireless keyboard and mouse. The back panel of the hardware module is populated with connectors to interface to all aspects of the sputtering system and to allow for easy future "plug and play" upgrades/expansions.
The Phase II-Au control system allows the user to operate in either the “manual mode” or the “automated processing mode”. In the “automated processing mode”, the user designs "process layers” which are then compiled and saved as a “process” to be executed with a single command. The system allows up to 104 unique user entry points which are accessible only by password, limiting access to a user’s process layers and thereby preventing unexpected corruption of a user’s saved processes. Special “soak layers” can be easily incorporated into the process. Adjustable time base Data-logging to a Microsoft Excel spreadsheet is standard. Remote preparation of new processes in a spreadsheet emulator format is available as an option.
The standard Phase II-Au control system will accommodate up to (3) DC power supplies, (3) RF power supplies, (1) 4-way DC switchbox, (1) 4-way RF switchbox, (1) DC Ion Source, (1) RF Ion Source, (1) Linear or Rotary Ebeam, (1) Deposition Controller, automatic selection of sweep pattern based on material (1) Hiden end point detector (4) process gases , (24) Valves/shutters, down stream closed loop automatic pressure control, substrate rotation , substrate tilting and indexing and substrate temperature control. Processes are aborted if plasma is not detected, substrate temperature, process gas or chamber pressure is out of range.